Company-wide carbon accounting: The importance of the Corporate Carbon Footprint
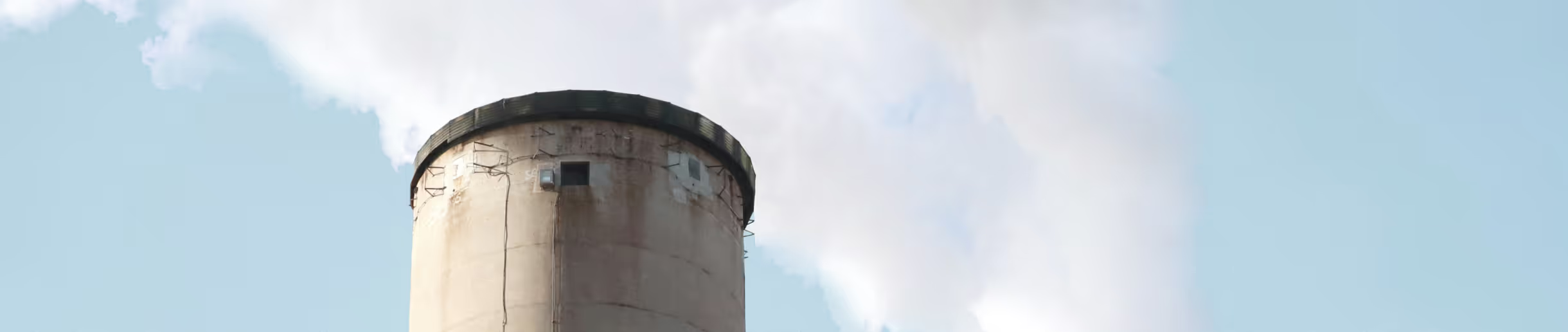
Why do we need a Corporate Carbon Footprint?
The growing pressure on companies to help curb global warming is leading to stricter requirements regarding environmental protection and sustainable value chains. Stakeholders expect companies to commit to efficient, resource-conserving processes in order to achieve the goal of the Paris Climate Agreement - limiting global warming to 1.5 degrees.
In this context, the importance of carbon accounting is underpinned by the Corporate Sustainability Reporting Directive (CSRD). This directive aims to increase the acceptance and standardization of carbon accounting processes and ensure that carbon emissions are taken into account in decisions by all stakeholders. The CSRD obliges companies to report on their greenhouse gas emissions by 2026.
This makes the Corporate Carbon Footprint (CCF) a valuable tool. The CCF makes it possible not only to identify a company's climate-related impacts, but also to quantify them. The comprehensive balance of greenhouse gas emissions of carbon dioxide (CO₂), methane (CH₄), nitrous oxide (N₂O), halogenated hydrofluorocarbons (HFCs), hydrofluorocarbons (HFCs) and sulphur hexafluoride (SF₆) forms a crucial basis for any climate strategy, as it enables companies to take targeted measures to reduce emissions.
How can the CCF be calculated?
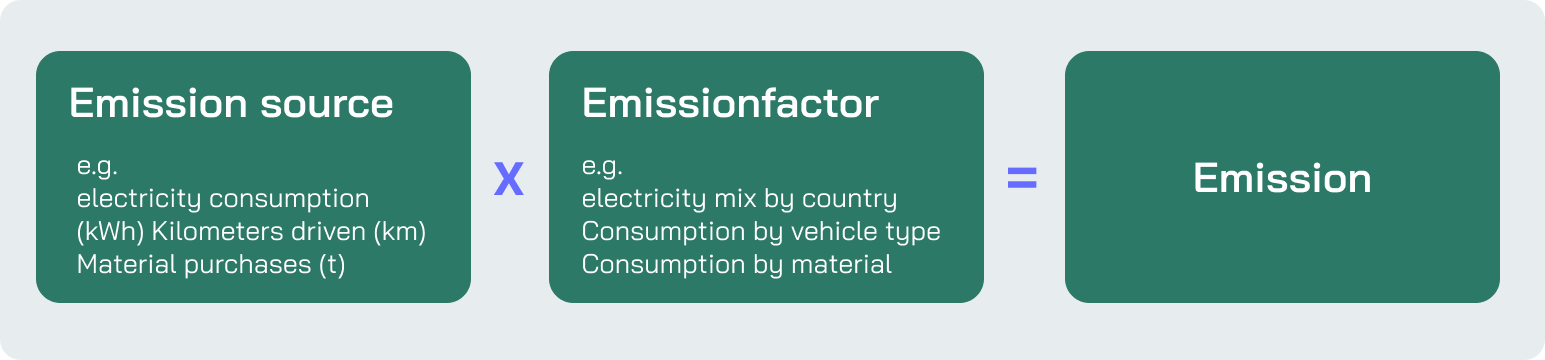
1. Source of emissions
The development of a carbon footprint or greenhouse gas inventory includes all relevant emission sources in the context of an organization. The structuring and categorization of emissions follows the Greenhouse Gas Protocol (GHG Protocol), an internationally recognized framework for recording greenhouse gas emissions in companies. This standard differentiates emissions into three main areas, known as scopes. This classification enables a comprehensive recording and evaluation of all greenhouse gas-relevant activities of a company.
Scope 1
This includes direct emissions that the company controls itself. Scope 1 includes the following:
- Stationary combustion
- Mobile combustion
- Fugitive emissions
- Process emissions
Scope 2
This scope includes indirect emissions resulting from the procurement of energy, such as
- Electricity
- Electric vehicles
- Purchased heat, steam & cooling
Scope 3
These indirect emissions include those that arise in upstream or downstream processes in the value chain and are not directly controlled by the company.
Examples of this are
Upstream
- Purchased goods and services
- Capital goods
- Fuel and energy-related emissions
- Transportation and distribution
- Waste
- Business travel
- Employee commuting
- Rented or leased property, plant and equipment
Downstream
- Transportation & distribution
- Franchises
- Utilization of products sold
- End-of-life of products sold
- Further processing of products sold
- Rented or leased property, plant and equipment Investments
Out-of-Scope
Out-of-scope emissions include biogenic CO₂ emissions and refer to greenhouse gases or pollutants that are not captured or regulated in a specific system or context: If a regulatory framework aims to control emissions from a specific industry or sector, any indirectly generated emissions or those outside the boundaries of that framework are considered out-of-scope. For example, the combustion of biodiesel releases biogenic CO₂ (CO₂ from biological sources such as wood), which contributes to environmental problems such as climate change. However, this biogenic CO₂ does not have to be captured by the current regulations and the Greenhouse Gas Protocol, as only the gases CO₂, CH₄, N₂O, HFC, PFC and SF₆ have to be captured under the Greenhouse Gas Protocol (GHG). Biogenic CO₂ is therefore not taken into account as part of the CO₂e of the emission factor, but falls under out-of-scope.
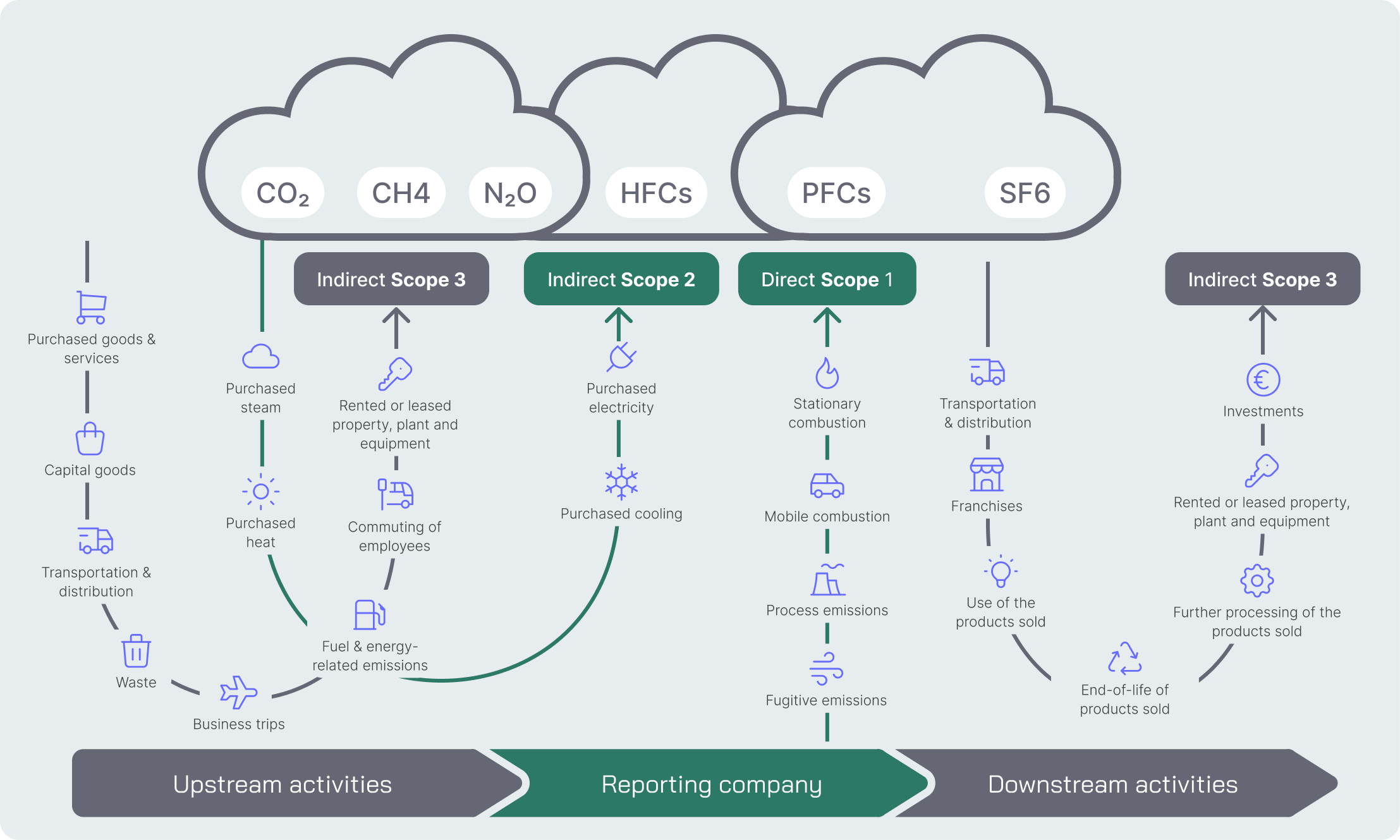
2. The Emission Factor
An emission factor is a measure of how much emissions, typically stated in kilograms or tons of carbon dioxide equivalent (CO₂e), are released by a specific activity or process. These factors are essential for calculating greenhouse gas emissions and help to quantify the environmental impact of different activities and industries.
Emission factors can relate to different sources and activities, such as
- Combustion of fossil fuels: the amount of CO₂, methane or other greenhouse gases released per unit of coal, oil or gas burned.
- Production of goods: Emissions generated during the manufacturing of a product, e.g. cement or steel.
- Transport: Emissions per kilometer for various means of transport such as cars, trains or planes.
Emission factors are indispensable in climate policy and environmental management, as they form the basis for emissions reporting and for the development of emission reduction strategies. They are also used to assess the effectiveness of environmental protection measures and to support companies and organizations in planning their climate protection strategies.
In order to calculate emissions accurately and identify suitable measures to reduce emissions, there are various methodologies for calculating emission factors. One of these methodologies is based on financial data and allows the emissions per unit of money spent on a specific activity to be determined.
1. Financial-Based Emission Factors
Financial-based factors are used to calculate the emissions generated per monetary unit spent on a specific activity.
The advantage of this method lies in the simplicity of data collection, as emissions can be calculated by tracking expenditure. However, there is also a disadvantage: the accuracy of the results can be low due to financial fluctuations.
2. Industry Average Emission Factors
Industry Average Emission Factors are used to calculate the emissions per unit of consumption of a particular activity. These factors, known as industry average emission factors or activity-based, indicate how much CO₂ equivalent (CO₂e) is released per unit of consumption.
The advantage of using Industry Average Emission Factors is the high accuracy of the calculations and the reasonable effort required for data collection. By using these standardized factors, companies can perform accurate emission calculations without excessive data collection efforts, but a disadvantage of this method is that specific consumption data may not be available for all activities. In such cases, the calculations may become inaccurate as the emission factors are based on general averages and do not reflect the specific circumstances of individual activities.
3. Supplier-Specific Emission Factors
Supplier-specific emission factors are used to calculate the emissions per unit of consumption of a specific activity. These factors are provided directly by one of your suppliers and indicate how many CO₂ equivalents (CO₂e) are released per unit of consumption.
The advantage of using Supplier Specific Emission Factors is the highest possible accuracy in the calculation of emissions. As these factors are specific to the products or services of a particular supplier, they can provide very accurate and reliable data for calculating emissions.
However, a disadvantage of this method is its low availability, as only a few suppliers can provide their own emission factors. This can limit the application of this method and lead to companies having to rely on less accurate average values if no supplier-specific data is available.
System boundaries define which process steps are included in the emissions calculations of a product, inventory or activity. They determine which processes are included or excluded in the emissions calculation and are crucial for the completeness and accuracy of the greenhouse gas inventory.
Importance of accuracy and consistency when using system boundaries
The precise and consistent definition of system boundaries is crucial to ensure the integrity and reliability of emission calculations. It is important to include all relevant processes in an emission factor and avoid double accounting. Standardized emission factor databases help to achieve consistent and comparable results.
What should companies look out for in carbon accounting?
- Relevance: Carbon accounting should adequately reflect the company's emissions and meet the information needs of stakeholders both inside and outside the company. This includes the definition of all company activities relevant to accounting.
- Completeness: All relevant emission sources within the defined inventory limits must be covered. This creates a comprehensive and meaningful corporate carbon footprint. It is important not to omit any emission sources, even if data collection can be challenging.
- Consistency: For traceability and comparison of emissions data over time, it is crucial to use consistent methods when collecting and calculating data. Changes in methodology or data sources should be documented transparently.
- Transparency: The carbon accounting process should be clearly and comprehensibly documented so that both internal and external auditors can understand the credibility of the data. This includes the disclosure of assumptions and precise details of the methods and data sources used.
- Accuracy: The reporting of emissions should be as accurate as possible to ensure that stakeholders can make reliable decisions based on the information reported. It is important to reduce uncertainties as much as possible.
How does Tanso help companies to calculate their Corporate Carbon Footprint?
The Tanso software not only enables the automated data collection of emissions from Scope 1-3, but also the management and optimization of your company's sustainability goals. Click here to find out how the software can support your organization in setting up a robust and audit-proof standard process with an audit trail.